Beri & Jasmine on tour
Beri and Jasmine were back on tour, and this time we took a closer look at automated weight and size checking as well as automated data processing systems – essentially, how we sort our parcels at the Buchs depot.
Shefik Sadiku, our depot manager, met us when we arrived and explained everything on paper first (it’s all quite complicated if you don’t work in the field) before we got to see the systems in the depot. Having worked at DPD Switzerland for over 22 years, Shefik knows the ins and outs of every process and procedure, from infeed to sorting to delivery.
FunFact:
Can you remember what song was in the charts 22 years ago? 😃
We hope there’s something there to suit your taste 😉 Now let’s get back on topic:
When a parcel arrives at the depot, what happens exactly?
1. Automatic size detection: what exactly is recorded?
At every infeed (an entry point where a conveyor belt transports parcels to the sorting mechanism) in Buchs, there is a camera with a scanner which measures the sizes of the parcels and pre-sorts them:
If a parcel is too tall (70 cm) or too long (140 cm), or if the size detector notices that something has an irregular shape (round etc.), the parcel is separated out so it can be sorted manually. This is done by an automated rocker which redirects longer or larger parcels to the manual processing point.
Why? Our system sorts a lot of parcels per minute, so for the sake of efficiency and keeping the conveyor belt running, only parcels that are of a certain size are sorted entirely automatically. They are also pre-sorted for safety reasons, because large, heavy or irregularly shaped parcels at speeds like these can pose a risk to the system, other parcels or even people. The volume measurement system used in the pre-sorting stage is from Ametras. We have twelve of these systems in Buchs, seven in Möhlin and three in our new Bern depot.
Did you know that we can sort between 5'500 and 6'000 parcels per hour?
2. Let’s say the parcel has standard dimensions – what happens next?
The parcels ride the conveyor belt through our digital measurement and weighing systems (those are the two large blue boxes you can see in the video). We have these boxes on the north and south side after the infeed. Every parcel goes through these boxes so that it can be assigned and sorted correctly.
3. What actually happens in these ‘blue’ boxes?
Each of these blue boxes contains three cameras which capture every angle of the parcel, as well as its size and weight, and add the data to the digital system. This data is merged with the information on the parcel label (the consignee, service and routing details). However, this first requires the consignee data to be provided by the shipper. Once it has all of this information, the intelligent sorting mechanism (a proprietary system developed by DPD Switzerland and the heart of every sorting process in Switzerland) can determine what departure gate to send the parcel to, so it either ends up out for delivery or being transported to another depot. That is why it’s so exceptionally important that shippers send us the data. Without the data, we cannot process the parcels with maximum efficiency.
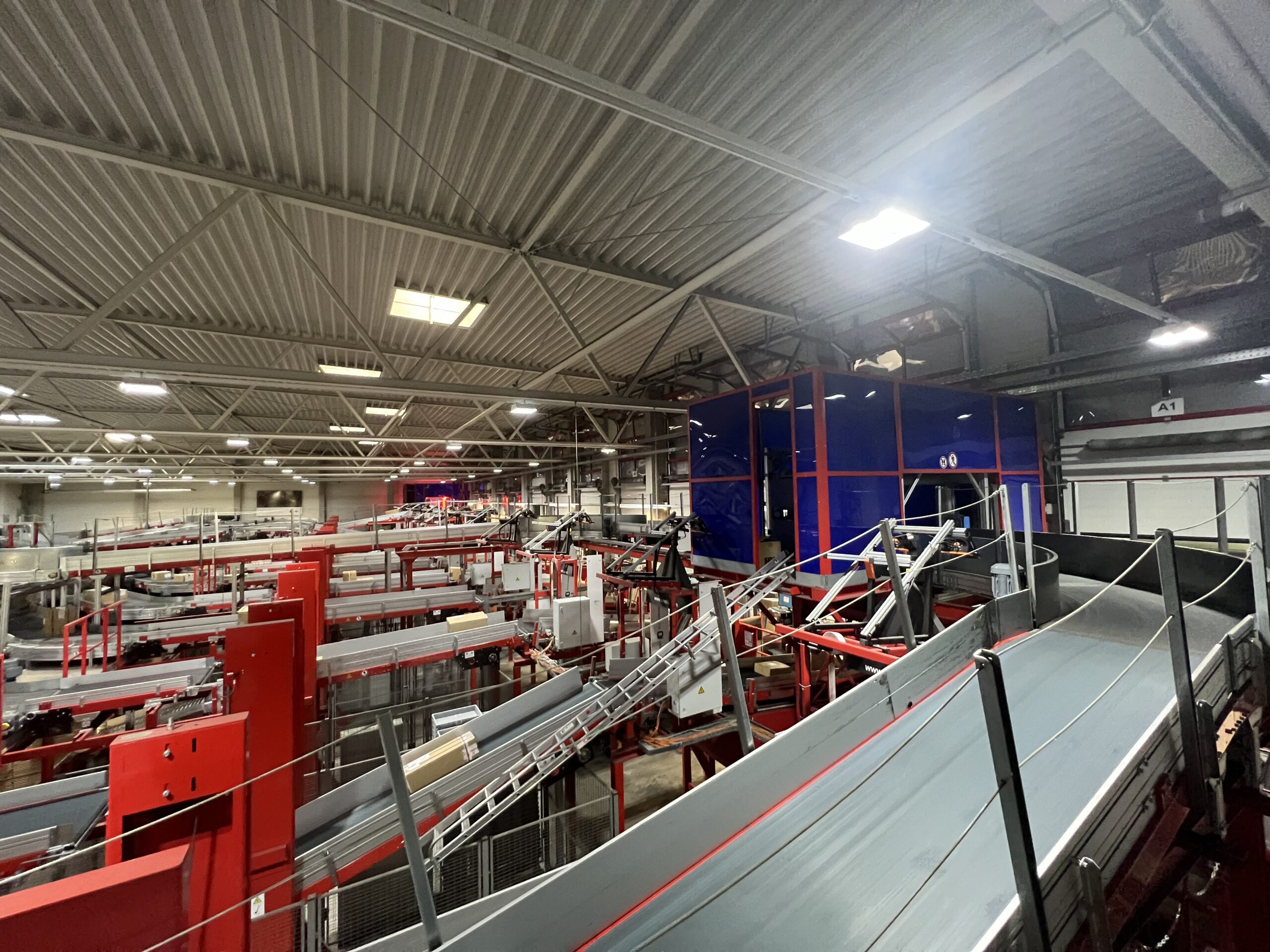
4. Where are the ‘blue’ boxes used?
According to Benjamin Bieber, our Senior Project Manager IT, the digital measurement and weighing system is very reliable. The advantage of the system is that it records not just weight or size, but both sets of data. We are currently using the digital measurement and weighing systems in Buchs because the blue boxes have something of a sensitive requirement. They need space because the section of conveyor belt has to be longer so that the parcels are far enough apart.
5. How good is our data acquisition exactly?
Michal Malach, our Depot IT Maintenance team leader, says that our data acquisition rate is 97 % accurate. In future, we hope to measure each parcel multiple times. As no measurement has a 100 % data acquisition rate, we can perform multiple measurements to improve the accuracy.
In any case, Michal and/or his team are notified immediately if something stops working or goes wrong in the systems. Essentially, he sits in the command centre and is responsible for the automated systems and for acquiring all the necessary data, not to mention processing and using that data.
To sum things up:
‘The parcel is sorted’ – it always sounds so simple, yet DPD cannot process this enormous number of parcels automatically without an absolutely immense amount of groundwork. It takes infeed staff who place the parcel on the conveyor belt properly, with the label facing upwards, at the very start. By the way, the Buchs depot has twelve female employees – girl power! The systems and technical aspects then have to work flawlessly so that everything can be recorded, processed and sorted. We must admit that we were unable to keep up during the deep dive into the servers and various systems and correlations. Nevertheless, we understand the principle. 😊
It also takes around 90 depot staff to sort the parcels correctly every day. The Buchs depot is the starting point for 130 routes on which parcels are delivered to consignees, so we should also spare a thought for the dispatchers who actively assist our drivers.
We hope that we haven’t confused you and that we’ve managed to offer a few insights into the complexity of our depot and the parcel sorting process.
Please get in touch if you have any questions or other feedback.
With warm regards,
Beri & Jasmine
PS: We hope to shine a light on the returns process in the near future... See you soon!